Instrument Repair to Orthopaedic Implant Manufacturing Standards
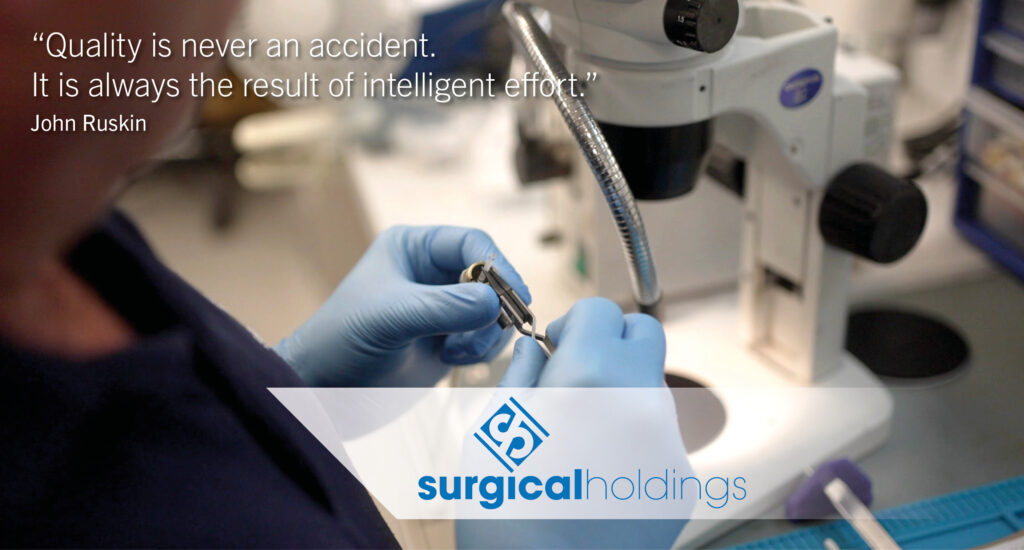
In celebration of Surgical Holdings’ 35th anniversary year, we are delighted to offer an exclusive behind-the-scenes glimpse into our state-of-the-art workshop in Southend. This week, we want to shed light on the exceptional quality that sets our surgical instrument repair apart from the rest. In this Q&A, our Managing Director, @Dan-Coole, delves into the intricacies of our processes and commitment to ensure your patients get the instruments they truly deserve, all while ensuring your hospital gets the best value for money.
“Quality is never an accident. It is always the result of intelligent effort.”
Q. Why is quality so important when it comes to surgical instrument repair?
The quality and functionality of surgical instruments play an absolutely crucial role in ensuring the highest standards and outcomes for patients. When surgical instruments are repaired to high standards, we ensure that they maintain their optimal performance for the surgeon, which is absolutely essential for achieving precision, reliability and safety during surgical procedures. Ultimately, this directly impacts patient safety. Materials, craftsmanship and quality control are all important factors in determining the overall quality and grade of an instrument. A hallmark of quality instruments is also their durability and longevity, and these are qualities that we continually strive for.
At Surgical Holdings, we’re acutely aware that the instruments we manufacture and repair are responsible for saving lives. That’s why we go the extra mile to repair our instruments to the highest standards, so we can provide surgeons with reliable, fully functional instruments that they can trust implicitly.
Q. What’s the Surgical Holdings approach to surgical instrument repair?
As a manufacturer of orthopaedic implants adhering to Class IIB standards, we understand the importance of precision, flawless traceability and strict adherence to quality. This same meticulous attention to detail extends to our repair services, ensuring that surgical instruments, scopes, and other devices are restored to the same high standards using our expertise, knowledge, quality materials, and refined processes.
An important testament to our commitment to quality is our accreditation to ISO 13485 through our medical devices notified body SGS, the same assessors that accredit sterile service departments. Although there are cheaper options that are not notified bodies, we feel this standard is essential.
We are dedicated to providing not only high-quality instruments and products but also ensuring that our repair services stand out as the best in the UK marketplace. We have a profound commitment to excellence. There is no compromise, we believe instruments should be repaired with the same care and value as they were originally manufactured – as we manufacture, we understand how to properly repair quality instrumentation.
Q. What makes Surgical Holdings’ repair service a cut above the rest?
Because we are an OEM (original equipment manufacturer), we have the unique advantage of manufacturing instruments ourselves. As an example, we are currently in the process of producing and launching our own rigid endoscopes. We believe our OEM expertise gives us a deep understanding of instrument design, construction, and functionality. This in turn enhances our ability to provide state-of-the-art repair services.
We also have instrument heritage dating back to the early 1900s. This experience has provided us with unprecedented knowledge. We’re passionate about what we do and are keen to pass that wealth of knowledge on to our customers. We believe it is important to educate and train others, to help them get the most out of their instruments – and so they last for many years.
Our commitment to quality is also evident through independent testing by the Cutlery and Allied Trades Research Association (CATRA). The results from this rigorous evaluation demonstrated a remarkable improvement in the performance and durability of scissors repaired by Surgical Holdings compared to those repaired using non-OEM techniques.
Q. Can you tell us a bit about the Surgical Holdings repair process and what it entails?
At Surgical Holdings, we follow a rigorous ten-step process for scissor repair. Our all-inclusive repair price covers various crucial aspects, including collection, admin and traceability, as well as essential steps like sharpening, setting, polishing, laser marking, passivation, packing and delivery. Each step is essential to restore the instrument to an “as new” condition, ensuring exceptional quality throughout the repair journey. We take pride in offering a quality alternative to repairs offered at absurdly low prices. While cheap repair options may be tempting, we firmly believe that our comprehensive ten-step process guarantees reliable and lasting results, as opposed to the quick fixes often associated with low-cost repairs.
We maintain strict standards by having our products serviced and repaired exclusively by our in-house team. We also recognise that the busy sterile services department may not have time to test repaired instruments before use, and our in-house testing is standardised to German DIN testing materials, ensuring all freshly repaired instruments are returned to our customers in an “as new” condition.
To make the process easier for customers, we’ve also developed Surgifix – an innovative web-based surgical instrument repair portal that allows the whole repair process to be arranged and managed remotely, offering a seamless experience for input, tracking, and analysis of customers’ repairs and data.
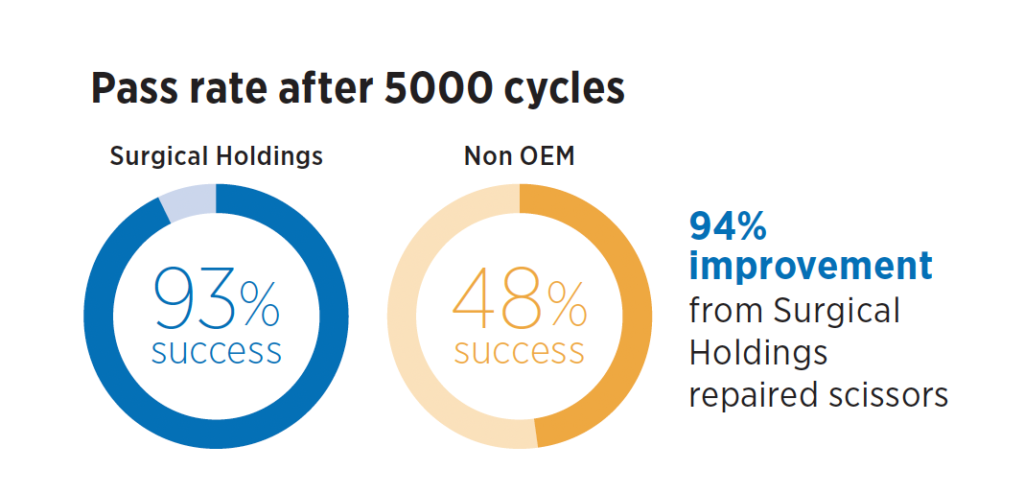
Q. How is the manufacture of Kirschner Wires related to the quality of repairs?
We’re proud to manufacture Kirschner wires at our facility in Southend. These orthopaedic implants are certificated under the Medical Device Directive and UKCA to Class IIB, which is a higher risk classification than Class I instrumentation and requires more stringent auditing and traceability in relation to materials. We apply these same standards to our surgical instrument repairs, ensuring the correct use of materials and traceability back to the original batch of raw material.
Q. What makes Surgical Holdings the go-to partner for surgical instrument repairs?
We understand the pressures that hospitals face when it comes to managing tight budgets. It can be tempting to choose a repair service solely based on a cheap repair price. However, it’s essential to consider the long-term implications, particularly considering value, product performance and total life cost.
While it may seem cost-effective at first, cheaper repairs often lead to more frequent maintenance needs and additional expenses with more frequent replacements. In the end, the initial cost savings end up being outweighed by these additional costs. By investing in high-quality instrument repairs, hospitals can achieve substantial value and ensure the longevity of their equipment. It also enables hospitals to focus on providing top-notch patient care without disruptions caused by faulty or poor equipment, which are costly to patients.
At Surgical Holdings, we take great pride in our ability to offer premium-quality instruments and repairs. We also encourage customers to actively participate in inspecting repairs, challenging the repair methods and evaluating these both through longevity and surgeon feedback. This transparent approach allows customers to have confidence in the quality of our repair work.
At Surgical Holdings, we not only manufacture top-quality surgical instruments; we use the same skilled technicians to repair and refurbish broken or worn equipment. Check out our full range of surgical instrument repair services: https://www.surgicalholdings.co.uk/services.html